Also telephoning home was a luxury, which, besides costly (however paid by Mr. Vriezen) also rare. Each request or booking had to be placed before 09:00 in the morning and in case the call would come through it wouldn’t be before 01:00 at night! More often than not the call wouldn’t come through at all and we wondered what the reason for that could have been. Here my knowledge of the Russian language came in handy. One day, Tony and myself had booked a call to talk to our wives; his in Hinckley (UK) and mine in Schiedam. Upon returning to the hotel from the yard we went to the telephone exchange room (which was officially not allowed) and I asked the old operator (lady, wrapped in blankets) whether or not our calls would come through that night. She informed us that my call would but the call to Hinckley couldn’t be made, since the cable between Holland and England was damaged. I told her that I couldn’t believe that and she then told me that Moscow didn’t have an English-speaking interpreter available. When I said that Tony and his wife both spoke English and were in no need for an interpreter she smiled and said: “Oh, you, bandit, you know very well that here in the USSR they must make sure that only good things are said and in case something bad would be said the interpreter would disconnect the call.” And she was not kidding!
One day we met a group of German tourists who also stayed in the hotel. They heard us speaking Dutch and English and apparently they were very enthusiastic and choose to tell us all about the enormous progresses made here in the USSR. Like that beautiful drilling platform they had visited that afternoon. A real gem of technology, they called it. Mr. Vriezen they informed them on the reason of our presence in Baku!
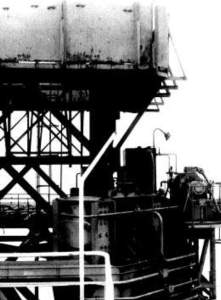
After the completion of the commissioning of the jacking systems and the welding of the first additional leg sections, I was asked to set the four legs on the bottom. They now were our anchors and we no longer depended on the poor mooring wires the yard provided us with. This was my first real jacking operation! The second leg sections were installed and welded. After some small preloading the hull was lifted out of the water, high enough so that the welding on the hull could be completed. And the trip to the full completion of the legs (94 meters) continued.
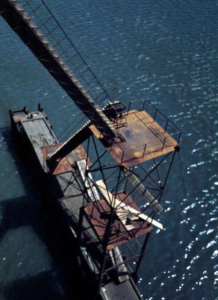
Therefore the leg sections, each about 65 tons and 10 meters in length, were hoisted onto the top of the legs, aligned and welded. Upon acceptance of the welding tests the work platforms were disconnected and brought to and installed on the top of the last leg extension. The hull was then jacked up so that the top of the jacking structures was just below the welding platforms. At first our access to the platform was through a gangway. Then, when higher, through a stair case tower and then the gangway. But when we were really high up the yard installed a complete drilling tower from which the gangway was installed to the deck. With some 10 meters of leg in the water this brought us up from the jetty to our deck some 65 to 70 meters higher. And all that time special water pumps were needed to provide us cooling water for the generator diesels (and other) and when the wind came from the North the dumped cooling water sprayed over our access, and the passing over the stairs of stair tower and drilling tower was a wet job! But not as bad as when they dumped the contents of our sewage tank!!
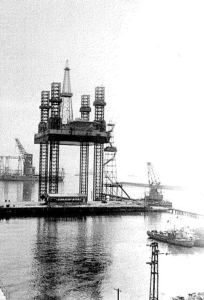
For the “final height test” we had to climb to the end of the leg. This was planned to be done during day light, but like almost always later in my carrier, by the time all the shore connections were removed, the gangway pulled onto the deck, all required personnel on board, etc. etc. it was almost dark when the jacking started.
We made it to the top without further problems. But during the second “pontoon lowering” stroke I noticed a slight glitch on the pressure gauge connected to the upper part of the jacking cylinders of leg #4. I stopped and Tony and I went to leg #4 to check. We soon found that the wide spray of hydraulic oil, which made our approach to this leg rather slippery, came from a blown o-ring. This was bad luck, 15 indeed! On top of that the wind started gaining in strength. And all this at about 80+ meters above the water! In the dark! We managed to install a new o-ring and when pressurizing of the line didn’t show any leaking we continued jacking down.
The Lub Oil Problems for the “Werkspoor” Diesel Engines
After jacking down we were confronted with a new problem. Already for some time we had warned the client that the “Werkspoor” diesels required a change of engine oil upon reaching the 1000 (or so?) hour working mark. We were promised the supply of this oil, but for the acceptance of the locally supplied oil “Werkspoor” required proper certificates; chemical and technical analyses. They were promised but never supplied. (nor was the oil!) We were however shown a “marmalade jar” with a little oil and was proudly declared to be best engine oil in the world. But we insisted in receiving the proper certificates and thus . . . . we had a problem. In the end (after discussing this subject for at least a week!) Mr. Vriezen (and Gusto) agreed that we would supply the oil from Holland, providing we would receive all necessary support from the client (which was the USSR government!). In order to organize the supply and transportation of the oil Mr. Vriezen agreed to return to The Netherlands and since all work had ground to a standstill I was invited to join Mr. Vriezen. Mr. Vriezen had been in “The city of Winds” (Baku) for almost 9 months and I arrived there 7 months earlier! Also Herman Klumper, the ‘Werkspoor’ diesel mechanic, decided to return home. His replacement (Lou Snoek) had already arrived and appointed, after Herman completed his 6 months! But he fell subject to a very strange virus. He spent several weeks in the “Hospital for the oil workers” and now was only too happy to leave this place after just over 6 months and see his own medic in Amsterdam. The diagnosis was: lack of vital vitamins! Organizing the purchase and delivery of the oil was done in a record time. It was agreed that Mr. Vriezen and myself would return to Baku as soon as we received confirmation of the oil arriving in Moscow. That took 3 weeks! It took the oil much longer than expected to arrive at the yard in Baku. Nobody from the Ministry of Import had arranged for a means to load the oil drums into the airplane from Moscow to Baku, so they decided to transport the drums by train. But then they would need a forklift to load the train in Moscow (possible!) but also one in Baku to offload the drums from the train. And this prooved to be too complicated! So after many days the oil finally arrived at the yard in Baku by trucks all the way from Moscow!
In the mean time political Europe (even the World!) had been upset by the USSR invading Prague. Now, try to imagine how we felt. And “we” stands for everyone in our team, Dutch, English and German alike. For so many months we had endured the most irritating and awful remarks and corruption of our project. And now this: the treacherous attack on a foreign country. As a thief in the night! Not a fighting nation but a nation only protesting against the harsh oppression endured from the Soviets. We were enraged, really! But what could we do? Walk away from this project?! That would not be an option: we (16) couldn’t leave without our passports and we would leave a very important problem for our employer. So we stayed and waited some more for the oil to finally arrive at the yard.
A few weeks later we learned from “Radio Moscow”(in English) the real reason for the occupation of Prague. When you see that along the doors of your neighbor’s house some smoke rises into the air, you will naturally become worried. You will try to warn your neighbor. But he seems not to hear you, so you knock a little louder on his door. He still doesn’t react, so you knock the door down and extinguish the fire yourself! Now we knew!! As I already mentioned: we had to carry on and complete this project!
Testing offshore
As soon as the oil was finally supplied the diesels were dealt with and the “Chazar” could be jacked down into the water, legs pulled and fully retracted and the voyage to the “test location” could begin. For this jacking operation Mr. Hage had come to Baku, together with Ken Cowley of Keelavite. Tony Tufts, the regular Keelavite technician, also had returned to Baku from a few weeks at home. While we waited for the client to get it all organized some extra moral support arrived from Gusto: Mr. Guus Smulders, together with the IHC agent in Moscow, Mr. Huvelle, came to Baku for a few days. And from Mr. Huvelle we learned how wonderful life was in the USSR! That really everything was possible and available here! We were ready to “keel hole” him! But he proofed his point and within a blink he arranged for us beer, champagne and caviar. Yes, really: caviar! These Sturgeon eggs are produced and processed here in Baku, but NOT for the local market. For the Export only! Caviar must generate “hard currency”! But that night we enjoyed it all. Some night it turned out to be!!
When finally all the arrangements were made and the jacking operation could begin, it turned out that Mr. Hage had fallen down with high and unexplainable fever. He had to remain in the hotel and bed. Ken Cowley, however, joined us on board. Leaving the assembly site proofed trickier than we had anticipated. The water depth was only about 5.5 meters and the leg penetrations into the sea bed was an average of 4 meters. With a nominal draft of 4.5 meters it gave us only one meter, minus some spare of about 0.5 meter (at the ship yard much debris could be expected on the harbor floor). It would certainly take a lot of caution to get the legs free. In the closed environment of this shallow harbor we could neither count on some swell or waves to rock us free. But we managed, thanks to a lot of patience. Finally we were on our way to the testing site, some 50 km south (about 51/2 hours) and out to the open sea. It was only 6 meters deep and expected penetration of 5 to 6 meters.
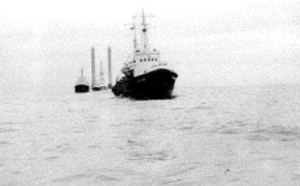
According to the contract we were obliged to proof the well functioning of all systems on board, including the drilling equipment and therefore had to drill a hole in the seabed with a depth of 2.000 meters. Since a drilling operation becomes hazardous when the drilling strikes gas, oil or any other combustible it was guaranteed by the client (USSR ministry of Oil) that the hole to be drilled would NOT strike any of such. And with such guaranty who could be worried?!
The location was only 3,5 to 4,5 hours sailing by little supply boats, but how far away that was we experienced when we became dependent on just these supplies for food. The name Baku means in the old local language “City of Winds” and the weather stations recorded an average of 296 days per year Beaufort 6 or higher. The Caspian Sea being an enclosed sea, the wind often swept up the waves in no time. It was therefore that a general rule was in effect: wind forces of 6B or more would keep all ships to the ports and as soon as the wind speed would drop to below 6B and this fact was reported to Moscow a message from Moscow would allow sailing again. So the little “supply boat” often waited for permission to sail out for many days. Often more than one week!
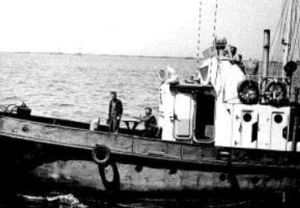
“Supply boat” is a too big name for the little ship. Actually it was a small crew boat with a cabin for 6 to 8 passengers and a mechanical rudder mechanism (wheel connected to chain and cables moving the rudder from port to star board), with a small open deck at the bow and one at the stern. On these open decks our supplies used to be stored from the moment trucks had transported them to the loading dock till the moment the boat crew had thrown them into a basket to be hoisted up onto our deck. Sometimes these provisions, such as raw meat and paper bags with bread, would lay in the sun for days before they could be safely stored into our refrigerators on board of “Chazar”. During the sailing trip to our location the waves often splashed over our provisions against which the paper bags could mean not much protection. Mr. Vriezen at one time even forced them to dump all the meat into the sea! They hardly had to push the rotting junk: it almost crawled over board by itself! This supply system often left us waiting on board and I often told the (true) story of us being fed on three whole chickens! Then I would follow with the information that this was for 40 persons! As much as Moza did her utmost, the quality of these food supplies was very low. I lost more than 15 kilograms; part of it I could miss, indeed, but . . . . . !
Our mailing address remained at the hotel “Intourist”, so at intervals one of us would sail the supply boat to the shore, collect the mail and return by following occasion. I have sometimes waited on shore for days and days, reporting daily at the offshore transportation office before returning to the hotel. During one of these trips to the shore the chain wheel broke off the steering wheel and the boat was rendered out of control and subject to the waves. Captain and all passengers fell sea sick and while I operated the throttle of the little engine the mechanic operated the mechanical steering boom inserted into the hollow end of the rudder shaft. This time the 4-hour trip took us almost 6 hours!
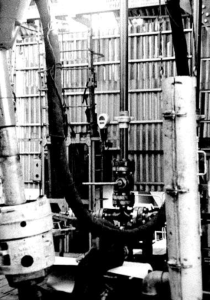
Finally we achieved the required drilling depth (1.996 meters was gladly accepted!). The string of drill pipe was broken down to 12-meter joints and fastened onto the pipe rack. Also all lose items of any importance were sea fastened and the loading sheet made up. After proper ballasting the platform was ready for jacking down, just waiting for the tugboats and Mr. Hage and Ken Cowley. However Mr. Hage was again knocked down by some kind of aggressive virus and he even ended up in the “Oil Workers Hospital”. So it was all up to me! We hooked up the mooring cables to the buoys and picked up some slack. I lowered the platform into the water and after giving the mooring system some tension I started with pulling the legs out of their penetration. Pulling the legs, penetrated some 10 meters, had to be done carefully. Pulling is achieved by increasing the draft but when that is done too drastically and some legs would “pop-out” the platform could easily end up with a too large inclination and thus jam the legs, which remain penetrated.
Therefore a little swell is usually very welcome. But that day the sea was like a mirror. Then only patience helps. When I explained to the captain of the ‘Chazar’ why it was taking me so long to get the legs free he immediately ordered two tug boats to run circles around us in order to make for some waves!!!
Job completed!
Once the legs had been fully retracted and the three tugboats hooked up and the mooring system released we were towed back to Baku. ‘Chazar’ was to be jacked up on its first official drilling-for-oil location, not far from “Neftiany Camni”, or “Oil Rocks”, North East of Baku. But first we were asked to bring the platform to a sheltered location in the bay of Baku. There the platform was to be loaded with the usual supplies of tools, drill pipe, casing, mud and other chemicals and, most important, with food supplies. This would take about a full week. Jacked up and preloaded properly we left the platform for the new owners and our whole team left for Baku. And I was proud to report to Mr. Hage about the job I had done. He was released from the hospital and had witnessed our performance from the balcony of his hotel room.
After taking on all necessary supplies we (Mr. Vriezen, Tony and me) moved ‘Chazar’ to its drilling location where it was jacked up and prepared carefully. However the penetration was a lot more that was anticipated (actually about 13 to 15 meters) and once we had it jacked up to its working position we had only about 3 to 4 meters of leg left above the jacking structures. Tony thought of something funny: he went to his cabin and put on the lifejacket, which he had found there. When he returned to the canteen and said “Good Night” to all of us, it frightened the captain so much that he reported his panic immediately to his uncle, the Minister of Oil in Moscow. We had to control ourselves to not burst out in laughter.
After the usual checking and survey of the jacking systems and the position of the platform the job was declared completed. A hand-over party was arranged, for which several big shots had flown over from Moscow. And like magic all kinds of luxury food and drinks were available. Even Caviar! And lots of Vodka!!
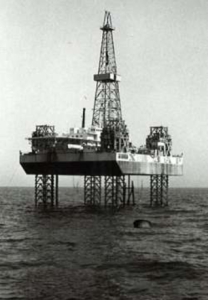
Our Russian counter parts thanked us for all the help and affords but one of them, an older electrical engineer, who spoke a little German, informed us that there had been one downside to the whole project and our cooperation. We wondered what that was. We could mention a dozen shadowy items, but were in a too good mood to mention any. We were then told that our Russian friends were hurt every time we called them “Russians”! They almost all originated from Azerbaijan or any other USSR republic and though they could all be called “Soviets”, they would NEVER be “Russians”. We were a little shocked. He told us this in German, but for sure some of the real Russians (from Moscow!) must have understood. But they just smiled! We apologized and promised our friend that we would call them “Azerbaijani” from now on! Another toast and everybody was happy again.
Three days later, on December 3rd 1968, we (Mr. Vriezen and myself) landed at the new Schiphol again. Tony had left Moscow a few hours earlier on a flight to London.
Warranty Service
During the following 1 1/2 years I visited Baku and the “Chazar” for two more short periods. Each time to support and supervise the jacking operations performed by Roma Rezaijev, the local engineer I had trained in 1968. The first time it was all arranged before I left for Moscow and Baku, but for the last trip I was asked to discuss the matter of the payment of my pocket-money with the representative of the Ministry in Moscow. I had to deal with this without the support of an interpreter. The deal with Gusto was $10 per day, but that caused some problems. I therefore was asked to accept the equivalent amount in Rubles. We agreed in 10 Soviet Rubles per day and since I was not allowed to take any of these Rubles out of the country I was happy to meet Mr. Guus Smulders again on my return to Moscow. And handed him these Rubles.
During my first warranty trip everybody on board of ‘Chazar’ was excited. A small transport ship with a crane came along side the ‘Chazar’ and would bring the long awaited ‘Werkspoor’ spare parts. They had been ordered more than a year ago! Interested in this offloading operation I watched it while hanging over the port side railing. I remember clearly that Mr. Machalov stood to my right side. The deck hands on the boat wrapped a single steel sling around the two big wooden crates, one on top of the other. I warned Mr. Machalov that two slings would be much better and safer, but he either didn’t understand me or just didn’t listen. And with just a single sling the load of about 300 kg was picked up and started to rotate, rotate and rotate, until the steel wire was fully unwound and the strands started to part. The crane driver saw it happening and in order to let the load drop on the deck, rather than into the water, he swung the boom back to the boat. Thus it happened that the two crates dropped onto the edge of the boat and like an explosion the crates burst open and the so long wanted spare parts dropped into the Caspian Sea. Mr. Machalov cried and cried big tears!
By the time divers could go down and look for the parts it was a few days later. The quickly worsening weather and seas prevented any diving sooner. This was before we left this drilling location. Remember the leg penetrations of about 13 meters, of which the top was some thick soup. No way they would even be able to find a complete diesel engine, let alone small things such as bearings and camshafts. The last time I visited ‘Chazar’ we moved it to a location in the eastern part of the Caspian Sea, near “Krasnowodsk”, or City of Red Water. We weren’t granted a visa for this USSR republic, so we had to return to Baku sailing with one of the tugs.

And on 20 December 2005 I shot the following photo of the “Chazar” and its 4 clones, laid up just south of Baku. Notice that on the clones (copies of the original) the legs look much heavier than on the original. Probably since the high tensile steel used by Gusto to construct the legs (HSB) was not available when the clones were built. To achieve the same (or similar) strength the wall thicknesses had to be increased, thus making the legs more heavy. Thus also causing the hull to increase little in size.
Report and memories assembled and written up in December 2014
by: Alex Wittmaekers
Service / Jacking Engineer of IHC Werf Gusto
Stichting Erfgoed Werf Gusto
Laatst bijgewerkt op: 22 januari 2023